Sweatshops thrive in the garment industry
March 2022
By Clare Bailey
The structure and organisation of the 21st century garment industry in the UK is determined by the online fast fashion business, where demand is volatile and articles of clothing are designed to be worn once then thrown away. Furthermore, competition between suppliers drives prices and wages down to levels parliamentary committees profess repeatedly to be shocked by. Manufacturers win orders and survive by being able to respond rapidly to brand buyers, via suppliers who place the orders directly with the usually very small factories and often with homeworkers who appear on no one’s payroll. According to Unite the Union, labour exploitation in the garment industry is at an all-time high, which is saying something. Employment practices that would have been familiar to workers in 19th century factories are widespread in today’s industry.
A HISTORIC INDUSTRY
Britain has a long history of producing textiles and clothing. It began by exporting wool in the 8th century, and by the 12th century these exports to weavers in Flanders were creating huge wealth, not least for the Monarchy through taxation. For over two hundred years wool was the most important component of the English economy – sheep took over the landscape from the Pennines to the South Downs. The Highland Clearances - clearing the way for sheep - inflicted famine and destitution on the population of Scotland in the 18th and 19th centuries.
In the late 18th century spinners and weavers, working alone at home or in twos and threes, were forced by employers to work at looms in water-driven mills. Then as steam power took over and the first industrial machines were developed, work moved into factories where conditions were brutal. The cloth industry grew fast: in 1813 there were 2400 power looms in Britain, by 1850 there were 250,000.
Until the 19th century ready-made clothing had been restricted to military uniforms; then standard sizing began to appear and the invention of industrial sewing machines in the 1860s saw the beginning of factory production of clothing. By World War I the clothing industry was one of the biggest employers in the UK. The size of individual manufacturers, compared with textiles, was however typically small. In fact workers were often ‘outworkers’ doing piece work at home and records of employment were not kept. This remains the case today where the ‘sweating’ of mid-19th century clothing workers is replicated in cities where the industry is concentrated. Factories are small and investment low because the technology involved in clothes manufacturing has not essentially changed in almost 200 years. Machinery can’t easily replace human skill when dealing with a material as hard to handle as cloth and this fact has been the determining feature in the history and development of the industry.
Low investment means low productivity and the intensive exploitation of labour. As Unite the Union puts it: “...manufacturer’s wages are the highest single cost, thus in ‘high-wage countries’ clothing producers continually attempt to drive down wages for profit.” This was as evident in the 1840s as it is in 2021 where industry workers in Leicester routinely earn below the minimum wage and often as little as £3-£4 per hour.
HIDDEN FROM VIEW
By far the greater part of the industry today is spread across a few hubs in North London, Manchester and the East Midlands. Data from industry sources and the Office for National Statistics (ONS, March 2020) suggest it currently employs something in the region of 100,000 people. It’s impossible to be sure of the precise number of people working in the industry, however, because so much employment is off the record and because the numbers fluctuate all the time. The industry expands and contracts according to demand and – regulations being so poorly enforced – because it can.
In the same way, it’s difficult to be precise about the number of factories, workshops and manufacturers. One Statista chart shows the number of garment manufacturers over a10 year period between 2008 and 2017 remaining fairly steady at just under 4,000, close to numbers others give for 2021. Numbers are perhaps growing currently due to the expansion of online fast fashion in recent years – a trend that accelerated during the pandemic lockdowns. Other Statista research shows the relative size of about 5,000 manufacturers (including footwear) and the very clear clustering of high numbers at the smaller end of the scale. Roughly 3,400 of them have a turnover of under £500,000 per annum, which places them well outside the scope of the Modern Slavery Act 2015. According to M Shahbandeh, writing for the site in June 2021:
“In 2009, wearing apparel manufacturers in the UK produced a turnover of around 2.56 billion British pounds. Over the following six years this figure increased, reaching 3.38 billion British pounds in 2015. In 2019 the turnover of wearing apparel manufacturers declined, to around 2.44 billion pounds.”
ONS data at March 2020, however, shows a much bigger annual turnover of around £11bn and industry sources claim it exports between £7bn and £9bn worth of goods annually – these differences in data proving the point that all numbers relating to this industry should be read with a sceptical eye.
BOOHOO'S RUTHLESS TACTICS
Unite the Union argues it is not enough to blame exploitative factory owners for conditions in the industry: ‘Retailers’ purchasing practices create a race to the bottom culture in the industry through their demand for cheap prices, rapid deliveries and a punitive financial culture which imposes huge fines on producers [for late production].’ Prices are driven down at suppliers’ meetings with manufacturers – here is an account of one such meeting with Boohoo, the UK’s biggest fast fashion brand: “Boohoo holds weekly meetings at its Manchester head office, where suppliers bring samples to the product teams in a single room with 10 to 12 large tables. ‘It’s like a cattle market,’ says one person from a supplier who did not want to be named. ‘Say I’m the buyer, and [you’ve] just given me the price of this [dress] for £5. I will literally hold it up to the next table and say, ‘How much for that?’ and he’ll tell you £4. It’s ruthless.’”
This is the fast fashion model based on small batch orders with a rapid turnaround, that encourages unauthorised subcontracting by suppliers in order to meet the rapid production times and the volumes required. This in turn opens the door to the exploitation of workers and non-compliance in terms of working conditions. It also facilitates wage fraud in many forms, especially for the more vulnerable workers.
Boohoo owns PrettyLittleThing, Warehouse, Oasis, Burtons, Wallis, Dorothy Perkins and Debenhams. It has a value of £4.6bn and grew by a massive 44% in the early months of the pandemic as online shopping surged. It featured prominently in the news in 2020 when employers in poorly ventilated Leicester factories supplying the brand were reported by an undercover Sunday Times investigation to be making workers work through Covid illness and in dangerous conditions. It led to an independent review being set up in September 2020 and this in turn produced 34 recommendations including the publication of Boohoo’s long withheld supplier list.
According to Labour Behind the Label (LBL), an organisation campaigning for garment workers’ rights worldwide: ‘It has been reported by workers that many Leicester factories continued operating throughout the lockdown. The principal cause was sustained orders, primarily from the biggest brand sourcing from Leicester, Boohoo, which continued to operate and trade online. By the 22nd April, even before the lockdown on businesses reopening was lifted, factories were reportedly operating at 100% capacity.’ Operation Tacit, set up by Home Secretary, Priti Patel, in response to these investigations and an independent review, involving 4 separate agencies, has not brought a single prosecution.
In response to this attention, Boohoo finally produced its UK supplier list in March 2021. But it’s also possible a US threat to ban Boohoo imports due to its use of ‘slave labour’ had something to do with its compliance. The Leicester Mercury reported in March 2021 that US Customs and Border Protection believed there were sufficient grounds to launch an investigation into Boohoo.
MODERN SLAVERY
One of the pieces of legislation ostensibly designed to protect workers from the worst forms of exploitation in this and other industries is the Modern Slavery Act (2015). At a hearing of the parliamentary Environmental Audit Committee (EAC) in 2019, one MP asked Sarah O’Connor of the Financial Times (FT), who had been investigating the garment industry for some time and was giving evidence: “What is the success of the Modern Slavery Act (MSA) if you are telling us it does not have any impact? O’Connor’s response was straightforward: “When it first came out I was astounded by how weak it was because … you just have to write a statement. That is all you have to do. Even then, if you do not write the statement there does not seem to be any sanction.” Not only did the MSA permit companies to claim full compliance with its Section 54 on supply chain transparency simply by making an online statement on their own websites, it only required companies with an annual turnover of more than £36 million to make such a statement, thus excluding the vast majority of small clothing manufacturers from its scope. Unite has called for the complete revision of the MSA’s Section 54. The MSA was so widely acknowledged to be toothless that, by the time of the 2019 Environmental Audit Committee hearings, two reviews of it had already been carried out.
The target of the Modern Slavery Act at the time was less internal UK supply chains than those running from countries such as Cambodia and Bangladesh, where the Rania Plaza building collapse in 2013 killed 1,138 garment workers and focused attention on conditions in clothing factories supplying UK brands. In fact, the loose terms of the Act and the lack of enforcement may have been incentives for the ‘re-shoring’ of business noted by the parliamentary Environmental Audit Committee in 2019. Many companies have moved business back to the UK, where conditions are ideal for fast fashion in other ways too - supply chains are far shorter and response times correspondingly faster.
The fact that UK garment factories are operating freely in unsafe conditions and that there are confirmed reports of workers not being paid at all for work done is well known, as is non-compliance, not only with the MSA but also with other employment legislation. There is evidence found by PricewaterhouseCoopers in their compliance review of the MSA that 70% of companies large enough to be required to comply had missed at least one of the 6 areas that government guidance recommended should be addressed. A second review carried out in 2019 found that 40% of eligible companies had not been complying at all.
For garment workers in the UK the situation is bleak. The Modern Slavery Act is not the only inadequate piece of legislation. Other laws and regulations are also routinely ignored without sanction. Basically labour law doesn’t apply. There are many different enforcement agencies involved but they do not cooperate where necessary and they have inadequate powers to follow through on what they find. There has been no shortage of investigations into and reports on the industry in recent years – the conditions 1000s of workers have to endure are, as the FT’s Sarah O’Connor put it, ‘an open secret’. Fixing Fashion, the report produced by the Environmental Audit Committee in 2019 following its hearings, made many specific recommendations for addressing the problems they had found. The Tory government rejected all of them.
HMRC, responsible for tackling minimum wage offences, irregularly publishes lists of companies found to be underpaying garment workers along with the outstanding fines owed but no company has been prosecuted for non-payment. The Gangmasters and Labour Abuse Authority (GLAA), set up in 2005 after the drownings of cockle pickers in Morecombe Bay in 2004, published a ‘protocol’ on the apparel industry in 2018, calling for a more joined up approach between agencies and better information gathering generally. It announced it was focusing its attention on the textile industry in 2021, recognising it as ‘a high-risk industry for labour exploitation’ but it has no real powers and even has difficulties securing warrants to inspect factories. The Labour Market Enforcement Board report summary for 2019-20 does not even name the clothing industry as one of the high-risk areas for labour exploitation – it lists: car washes, agriculture, hospitality, construction, care, shellfish gathering, nail bars, poultry and eggs, warehouses and distribution centres. And yet buried deep in the report is a footnote on the Leicester garment industry naming numerous investigations and reports over the last 20 years – all of which led nowhere.
VULNERABLE WORKERS
‘A £4 dress is only a ‘bargain’ because someone somewhere is paying the true price.’, says Labour Behind the Label. It’s report ‘Boohoo and Covid-19’, focused on Leicester, describes the workforce as follows: ‘It is estimated that most garment workers are from minority ethnic groups. Around 33.6% were born outside the UK (e.g. from India, Pakistan, Bangladesh but also Somalis and increasingly Eastern Europeans). These workers are vulnerable to abuse as a result of their immigration status, language skills… and higher unemployment rates. There have also been numerous allegations of links to modern slavery and trafficking.’
The lack of documented resident status or entitlement to work means many workers accept jobs without formal contracts or minimum wages. This also contributes to a situation where they are unable or unwilling to speak out about labour rights abuses for fear of deportation. The UK Home Office hostile environment policy targets and punishes migrant workers as opposed to addressing exploitation and promoting systematic change in labour malpractices. Unite has called for ‘firewalls’ between immigration enforcement and services for the support and protection of garment workers.
Workers living as precariously as this, even those with the right to live and work in the UK, are understandably reluctant to draw attention to themselves by joining a union and union membership is consequently very low. Globally it is estimated that fewer than 10% of garment workers belong to a union and after her investigation into the Leicester factories Sarah O’Connor said ‘I did not see much evidence of trade unions.’ When asked directly at the EAC hearings whether Boohoo’s factories recognised unions, the company’s co-founder Carol Kane said there was ‘no real reason’ for them, ‘there does not currently appear to be a demand’ and that they had an ‘employee forum’ instead. When pressed, Kane added that ‘if the workers would like it’ Boohoo would recognise a union. Since 2020 the TUC Midlands has been working with Leicester Trades Council and brands ASOS and New Look (and other brands though not, it seems, Boohoo) to establish Workplace Support Agreements, which guarantee unions access to garment workers to recruit. In its report ‘Fixing Leicester’s Garment Industry’ the project was hoping two outreach workers would start work in November 2021. So, more ‘fixing’ to come.
That so many clothing manufacturers have been re-shoring their business in recent times should tell us as much as we need to know about how things stand, for this industry and the diminishing UK manufacturing sector. Far from being the ‘world-leading’ high tech economy projected by government propaganda, the reality is that the UK is a low wage, low productivity economy with businesses given a free hand to exploit skilled workers as they please and to break the law with impunity
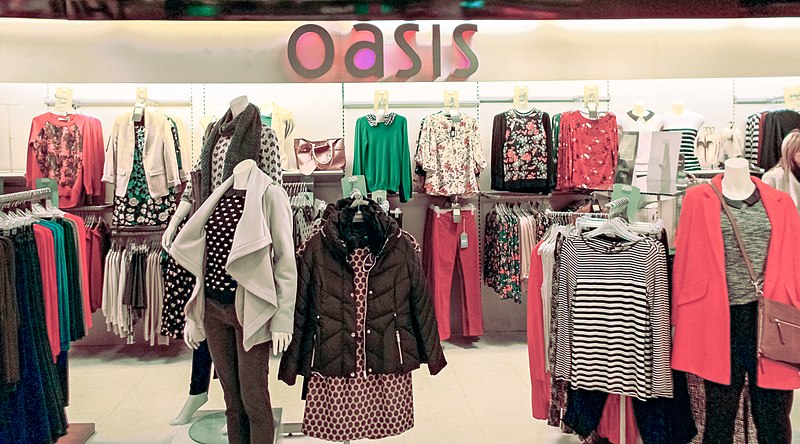
Fast Fashion photo by A P Monblat
Machinery can’t easily replace human skill when dealing with a material as hard to handle as cloth and this fact has been the determining feature in the history and development of the industry.
These workers are vulnerable to abuse as a result of their immigration status, language skills… and higher unemployment rates. There have also been numerous allegations of links to modern slavery and trafficking.
The lack of documented resident status or entitlement to work means many workers accept jobs without formal contracts or minimum wages.