Cost of building and repairs escalates
By Pat Turnbull
Councils, housing associations and developers are complaining that the costs of building and repairs have risen at more than the rate of inflation. Kate Henderson, the Chief Executive of The National Housing Federation which describes itself as the voice of England’s housing associations, said in an article of 26/8/22 entitled ‘Housing association costs rising faster than inflation’, that ‘This is…on top of the pressures of building safety cost and the cost of retrofitting homes.’ Building safety includes changes resulting from long overdue legislation to partially reverse the dangerous results of governments ‘cutting red tape’. Retrofitting is being urged to reduce energy consumption and emissions. These are costly changes with inadequate extra government funding to finance them.
MATERIALS SUPPLIES AND LABOUR
Woodgate and Clark describe themselves as ‘a dynamic, highly responsive loss adjusting and claims management business with over 40 years’ experience’. (1) Their ‘Building repair costs update: July 2022’, published 15/7/22 reported that while only 1.5% of the UK’s imported construction materials came from the Ukraine and Russia, over 13% of steel reinforcement and over 9% of asphalt products came from these countries. In addition, the European market has been heavily reliant on imports from Russia so supply from the EU has become increasingly difficult. The article adds: ‘This is all compounded by the rise in inflation across all EU economies and nine of the top ten countries (China being the exception) the UK imports from, are European…Taking Turkey as an example, inflation is estimated to be 49 points higher than the 10-year average, and this is where 47% of the UK’s imports of radiators and 36% of steel tube comes from.’
The article reports: ‘Labour shortages in the UK worsened in the final quarter of 2021, with job vacancies hitting a record high of 1.2 million, more than double their level a year before, the ONS [Office for National Statistics] said. Construction job vacancies stood at 42,000, slightly down from the peak in Quarter 3 of 48,000 but just over 60% higher than Quarter 4 of 2019, before the impact of the pandemic and the UK’s exit from the EU.’ Apparently ‘incentives [are] being offered to potential apprentices such as financial assistance with training, guarantees of roles on completion of training and more advertising of the benefits of working in construction.’ However, there is ‘no immediate prospect of it having a positive effect’.
The article predicted ‘what we are likely to see: builders reluctant to provide a firm price because of material cost fluctuations, and difficulty finding a builder to do the repairs’ and recommended ‘One option is to minimise replacement and consider more repairs’.
IMPACT OF ENERGY COSTS
On 1/2/23 Woodgate and Clark published a further ‘Property Repair Costs Update from Nick Turner: January 2023’. Loss of Russian gas would affect materials manufactured in Europe and imported into the UK, ‘which is around 60% of all construction materials’. Wholesale gas prices had increased from 48.29p per therm in February 2021 to 592.56p per therm in August 2022.
The article reported that with the majority of construction materials being imported to the UK (60% from Europe and 20% from China) shipping costs are a major factor. The International Monetary Fund reports that shipping costs, which dramatically increased during the pandemic, remain high, which it puts down to the world economic situation and the war in Ukraine. Even transport costs in the UK have risen dramatically due to rises in fuel costs. Logistics UK reported that during 2022, compared with the previous year, overall costs had increased by 25% or more. Bulk diesel prices, diesel being about 30% of the cost to operate a vehicle, have risen by almost 50%.
Woodgate and Clark gave the glazing industry as an example. Clayton Glass is one of the UK’s largest and oldest independent glass producers and in a communication to their customer base they have estimated that the cost of their combined energy usage could potentially rise up to eight-fold. Around 20% of the cost of glass is gas used in the manufacturing process. Two Russian gas plants have now been sold by Guardian, one of the largest gas producers in the world, as a result of the Ukraine conflict. This has reduced the supply previously going into eastern Europe. There are alternative quotes from the far east and middle east but the cost of container shipping stops this from being a viable alternative. The Energy Surcharge on raw glass was introduced in late 2021 and at the time of the article reflected a premium on raw glass of around 25–30% additional costs. There is a world-wide shortage of PVB (polyvinal butyral) interlayer used in laminate glass. Changes in legislation in June 2022 (Building Regulations – Document Q) increase the need for laminate with no additional supply available.
In July 2022, plasterboard, used for quick installation of walls, partitions and ceilings, increased in cost by around 25% and is set for further increases in 2023. UPVC (unplasticized polyvinyl chloride) products, mostly window frames and sills, increased by 20% in 2022. Timber products, 90% of which are imported to the UK, increased between 15% and 20% in 2022. Plumbing and drainage products increased between 20 and 30%, clay drainage products by 50%, steel products by up to 22%, bricks and blocks by between 15 and 20%, concrete products such as kerbs by up to 25%.
Once again labour costs come into the equation. ‘Some UK manufacturers are bracing themselves for a potentially significant increase in wage costs’. This arises from the ‘shortage of skilled workers…trades…surveyors, engineers, site managers’ etc. But also: ‘All industrial commentators are saying that 2023 is likely to also see significant inflationary pressure on the labour market, as the cost of living crisis begins to put pressure on households.’
The report adds: ‘We must also be aware of situations where the less scrupulous may try and take advantage of this cost uncertainty and add costs purely for additional gain.’
IT COULD BE DIFFERENT
No doubt many of these imported products could be produced in the UK if the British capitalist class hadn’t run down Britain’s productive industries. Young workers could have been trained in the building trades if the UK’s building giants hadn’t preferred to employ ready-made workers from other countries, often already highly trained, especially from former socialist Eastern Europe, and willing to put up with poor wages and working conditions because of the lack of jobs in their own countries. Building colleges could have been kept open and publicly paid for, instead of being closed down. Wages and working conditions in the building industry could have been improved to make the industry more attractive. The EU could have resisted shooting itself in the foot by sanctioning Russia.
The end sufferers are likely to be tenants waiting even longer for essential repairs and refurbishment.
(1) Founded in 1978, in 2015 Woodgate Clark became part of the Van Ameyde Group, ‘a European leader in claims management’ with 46 businesses in 28 countries.
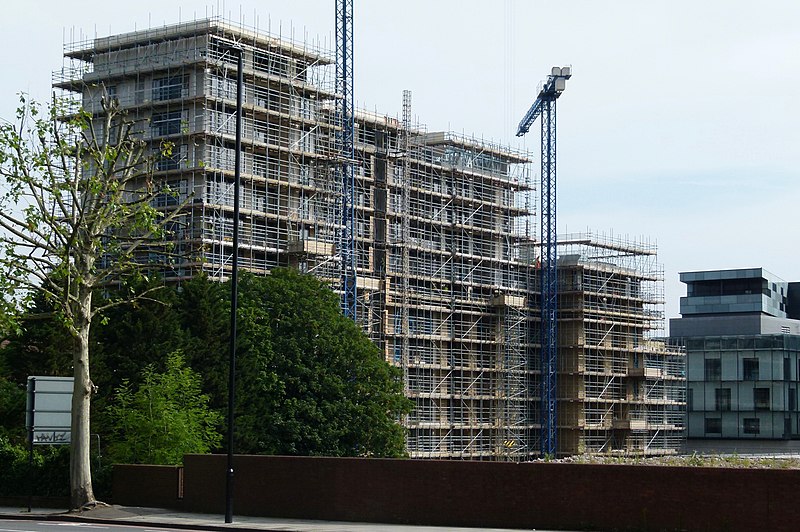
Building site in London photo by Kleon3
The end sufferers are likely to be tenants waiting even longer for essential repairs and refurbishment.